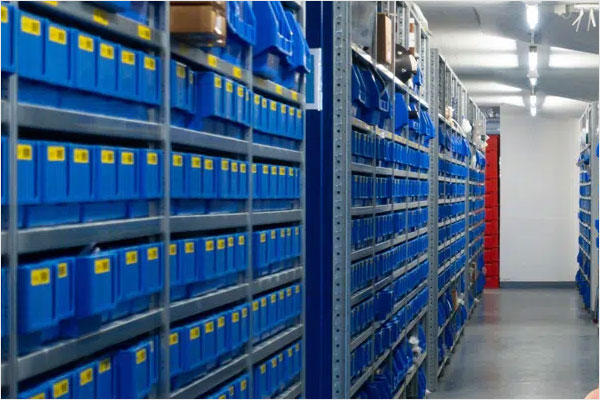
Once the product has been checked and is ready for dispatch, the main server sends the order to the printer in the packaging department, located one floor below. The order is scanned manually and all the packaging components required for dispatch are displayed. Through continuous process optimisation for better performance, once the packaging components for the order have been selected, an operating system employee scans the work order. The system sends a transfer command to the lift system and the shelf with the required documents moves to the access point where the compartment indicator shows the employee exactly where the packaging inserts and documents are located on the shelf. At the access point, the material number is scanned and registered in the system. After the retrieval transaction has been confirmed at the controller, the next item is brought to the access point – a sequential process that continues until the picking operation is complete. In order to speed up access, frequently required documents are stored on racks close to each other. When all the packaging elements are complete, they move along the conveyor system to the next level. This is where the finished product and the packaging are combined together. Once the packaging process is complete, the order is transferred to the transport department.
Label storage advantages
Optimal integration
In order to keep the travel distances in the system as short as possible, labels for construction materials are combined on specific containers according to the frequency of access. Labels for frequent pick and place operations are stored close to the access point. By integrating the storage of labels in the production process, companies can achieve higher retrieval speeds and productivity. Label storage is therefore the optimal link between storage and production.
High flexibility
Clear, coordinated allocation of storage locations means that labels can be found quickly and save valuable time in the order picking process. The integrated storage management system guarantees maximum flexibility and stock control.
Extended space capacity
The installation of automated, digitally-driven storage systems for Label storage extends the space capacity of your business, increasing efficiency and enabling faster retrieval, processing and distribution of critical materials.
Security, ergonomics, service
To retrieve the required product, the operator can enter a direct request on the microprocessor controller to automatically transport the item to the access point for retrieval at an ergonomic height. Strain injuries and work accidents can be prevented. Better protection and security for the operator and storage labels.
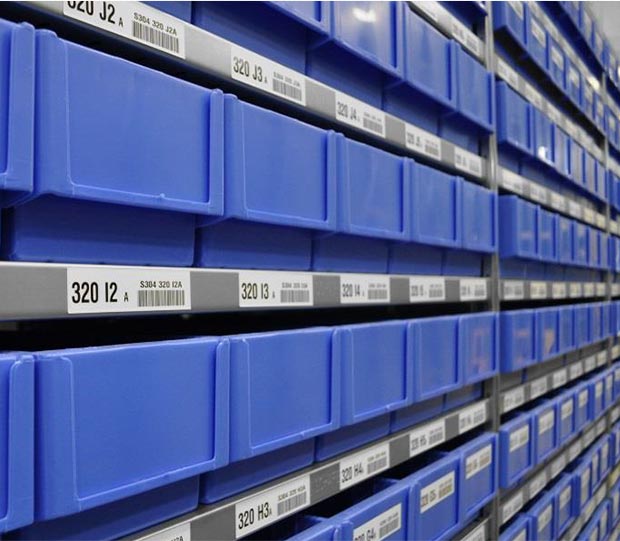