Plastic painting is to spray powder coating on the surface of the workpiece through a powder spraying device (electrostatic spraying machine). Under the action of static electricity, the powder is uniformly adsorbed on the surface of the workpiece to form a powder coating. The powder coating dries at a high temperature. Baking, leveling, and curing, and become final coatings with different effects (different types of powder coating effects); in terms of mechanical strength, adhesion, corrosion resistance, and aging resistance, the spraying effect of powder coatings are better than spraying technology. And in the case of the same spraying effect, the cost is also very high.
Plastic spray painting equipment structure
An electrostatic powder spraying system is mainly composed of a powder supply device, one or several electrostatic spray guns and control devices, an electrostatic generator (usually set inside the electrostatic spray gun), and a powder recovery device.
The working principle of plastic spray paint
The powder coating uses the principle of electrostatic spraying to adsorb the dry powder on the metal. After baking at a high temperature of 200°C or higher, the powder solidifies into a bright coating with a thickness of about 60μm. The surface of the product is smooth and flat, and the color is even. It has strong acid resistance, alkali resistance, crash resistance, and abrasion resistance. It can withstand strong ultraviolet radiation and acid rain for a long time without pulverization, fading, and shedding of the coating. The service life of powder-coated aluminum profiles under normal conditions is 30 years. The surface coating can ensure no fading, discoloration, or cracking within 5-10 years. Its weather resistance and corrosion resistance are better than ordinary aluminum, and it is color diversification.
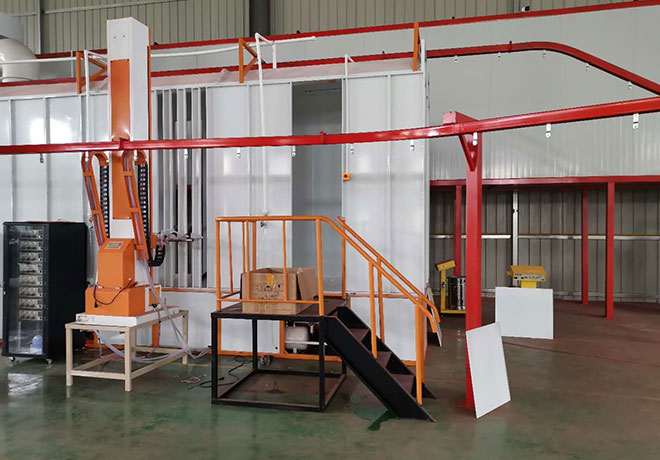