What is electrostatic painting?
The electrostatic painting uses the metal surface of the paint particles with positive powder in a special gun. Like a balloon clinging to the opening, it is attracted to a grounded surface and wrapped around a component such as a fence. In this way, a uniform coating can be formed, with almost no unnecessary spraying and waste.
This process has been widely used in the automotive industry and can also work for your home or business. It has been used in commercial applications for metal fences, railings, doors, and windows. Facts have proved that these large objects are difficult to transport to the powder coating workshop. Low overspray means expected less setting and cleaning.
How does electrostatic painting work?
It uses positively charged ions attached to atomized particles to work. These particles will be attracted to the grounded negatively charged metal. Just like a balloon charged with static electricity, the electric charge “sticks” colored particles to the object and distributes them evenly.
Besides, it is not like standard spray paint, there is no mess. It is done on-site with wet tones and requires 12 to 24 hours of curing, but it usually takes only a few hours to dry.
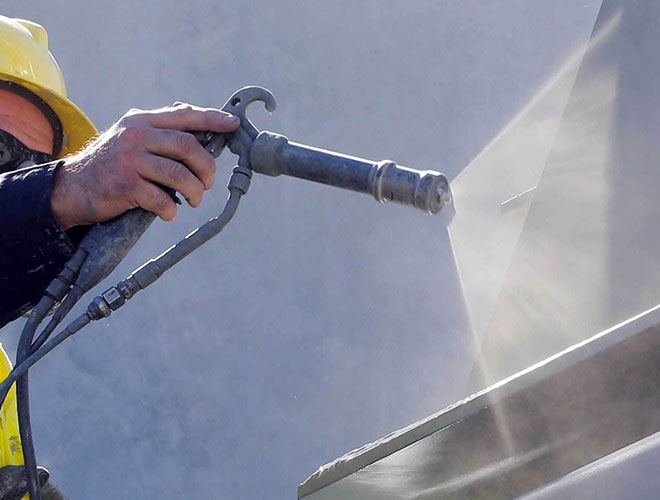
Why is an electrostatic painting gun more efficient?
The spray gun method charges the particles so they are attracted to the grounded metal surface. The particles will not blow over the object to be coated like a traditional spray but will move to the object to be sprayed, just like a magnet to metal. This end has a waste of less than 5%.
Why choose the DISK electrostat ic painting set?
High configuration components of DISK automatic electrostatic coating equipment
- The atomizer is made of the Taiwan S7 series, which has the characteristics of large torque, low noise, stable power balance (wind speed up to 60,000 rpm), fine mist spraying, and high paint rate.
- The electrostatic device adopts Taiwan high-voltage electrostatic generator, which is stable in operation and long in working life.
- The paint gear pump is equipped with a frequency conversion control system, the oil volume is digitally adjustable, and the paint discharge volume is stable and even.
- The coating tube adopts an imported Teflon explosion-proof coating tube.
- The elevator system adopts TECO low-noise 1HP variable speed motor, controlled by Delta frequency converter, and runs stably.
- Low-voltage electrical components adopt South Korean LG and Taiwan Tiande brands.
- Program-controlled components adopt the Japanese Mitsubishi brand.
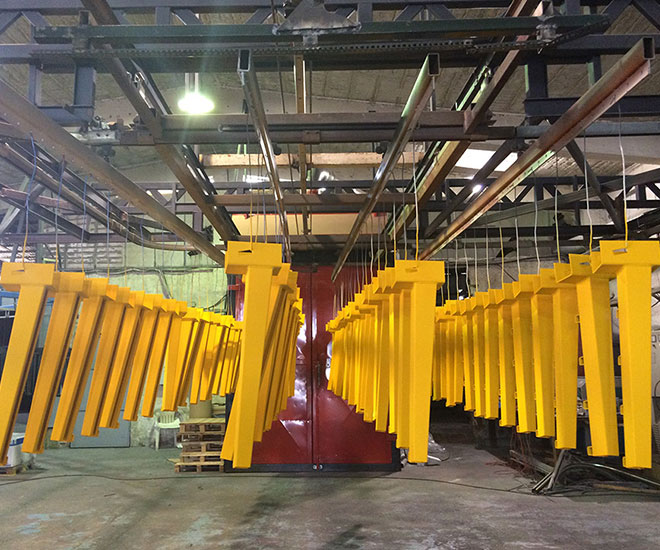
Advantages of electrostatic spraying of DISK automatic electrostatic spraying equipment
1. High quality
- Efficient: Fast paint and drying time means shorter downtime for your business, high rate of dead-angle paint, uniform overall paint, and stable product quality.
- Safety: The DISK equipment adopts the most advanced fully intelligent control system, which can directly output steps PWM control commands from the PLC, which improves the stability of the action, and the commutation is sensitive and accurate. For example to prevent leakage, overvoltage, overcurrent, overload, and automatic power-off.
- long-lasting: Seamless electrostatic spraying surface, new appearance, smooth touch, achievable surface quality makes equipment with years of experience look brand new. The bonding properties that may be produced by the electrostatic painting process can provide strong protection for corrosion, weather resistance, and mass use. Durability is especially valuable if your assets may be exposed to humid indoor or outdoor environments.
2. Cost savings
- Simple operation: Simple operation, regular training can be mastered after a small amount of training, which solves the problem of personnel management. The menu tool is easy to set up and can store 20 working menus, which can be selected at any time, which is convenient, fast, and accurate.
- Improve work efficiency: Similar to the air spray method, the electrostatic process makes the coating faster. Electrostatic sprayed paint dries faster than wet spraying methods and Electrostatic coating does not require a high-temperature oven. You no longer need to wait for several weeks for the room to be temporarily unused or the fumes dissipated. Normal business can be restored within a few days. Spraying operations can increase productivity by a factor of two, three, or more.
- Save raw materials: Reduce waste paint in the Electrostatic painting process. Compared with traditional operations, DISK automatic electrostatic painting equipment has a utilization rate of more than 90%, which can save 30%-60% of paint, which can greatly reduce production costs. Reducing waste can save $25 to $75 per gallon of paint, depending on the other high-pressure or air-assisted methods replaced by the electrostatic spray process.
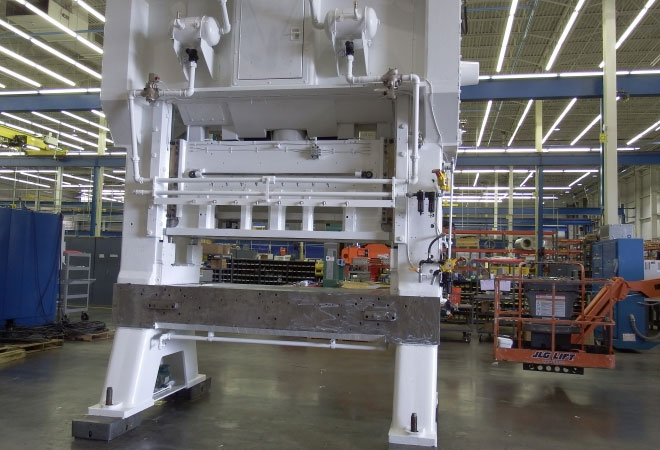
3. Long service life
Next time you consider discarding items that are still usable but look “old”, you can consider looking for a contractor that specializes in electrostatic painting. You may find that a recovery is a viable option. The right Electrostatic paint can extend your original investment and protect items that are still valuable for many years.
DISK automatic electrostatic spraying equipment has been recognized and affirmed by spraying manufacturers in various industries in various aspects of electrostatic paint system, performance, and environmental protection indicators. It has been widely used in metal, motor, bicycle, wood, furniture, motorcycle, auto parts, and other industries. Welcome to call for a consultation!