What is E coating?
E coating is an environmentally friendly e coating process that uses electric current to bond paint to metal products. The electroplated layer has high transfer efficiency, uniform film formation, and excellent corrosion resistance.
The parts undergo a pretreatment process, and then the cleaned parts enter a temperature-controlled, grounded steel storage tank lined with a chemically resistant dielectric material. After staying for 90 to 120 seconds in the aqueous electric coat paint solution to which a direct current charge is applied, the part is transported through a series of countercurrent penetrant flushing stages to remove undeposited paint. The parts are then transported to the oven to cure the e coat paint before unloading.
E-coat equipment: It solves the problems of high labor intensity, low efficiency, unstable paint quality, poor uniformity, and waste of paint in the spraying machine controlled by the construction personnel. The automatic coating equipment includes automatic lateral coating equipment that can be driven on the ground and hung on the back of the car. A control system is provided on the motor vehicle to control the longitudinal uniform movement of the motor vehicle and the lateral coating equipment of the automatic lateral coating equipment.
The automatic E-coat equipment can automatically spray a large area according to the set parameters, reducing the number of workers, reducing the coating efficiency, and the coating quality is stable and uniform.
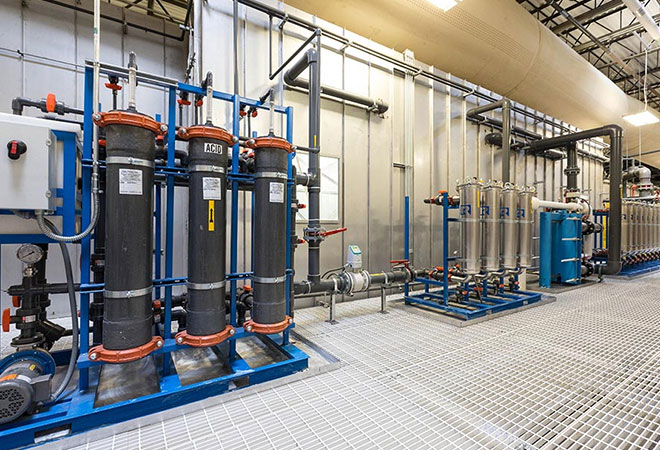
Composition of automatic electro-coating equipment
- The self-traveling coating line is mainly composed of the following parts:
- Pretreatment system (degreasing and descaling).
- Coating system (constant temperature, stirring)
- Automatic PLC transportation system;
- Hot air circulation drying system;
- Pure water preparation and spray system;
- Other pipelines, pump circulation, heating, and other auxiliary equipment.
The automatic e coating process
The process of the automatic electrophoresis production line is as follows:
Degreasing 4~6min→Degreasing 4~6min→Cleaning~1min→Degreasing 3~8min→Cleaning~1min→Neutralizing~1min→
Cleaning~1min→deionized water cleaning~1min→coating 1~3min→cleaning~1min→reactive cleaning~1min→curing at 110°C 30min→offline
The processing time of the whole line is short, the production pace is fast, the work efficiency is high, and the use cost is low.
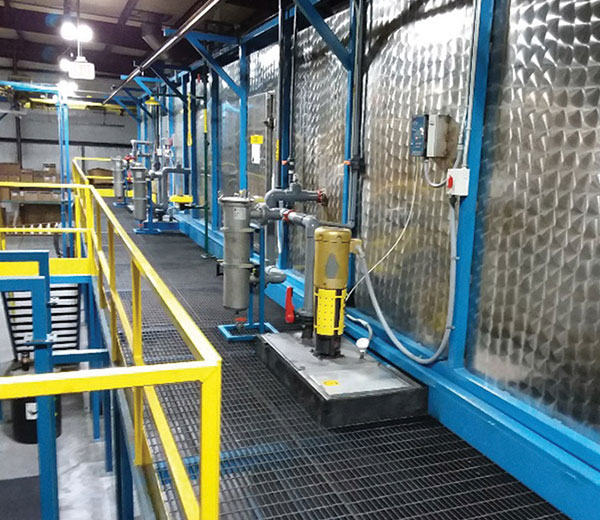
Benefits of E coating
- Immersion process: All surfaces in contact with the solution are coated. This means that even the most complex shapes can be completely coated. Parts can be packed more densely on the rack to increase productivity.
- Electrodeposition method: Electricity will cause resin and other components to deposit on the surface of the part. Controlling the current enables the application of a predictable and consistent coating thickness. This is essential if “colored” coatings are required, such as “brass” or “golden” colors on bright nickel or zinc alloys. Consistent color effects require consistent thickness.
- Water-based technology: There is no flammability problem during the construction process. In addition, there is no need to dry the parts after the water-based cleaning or pretreatment process. Using ultrafiltration technology, rinsing water can be extracted from the bath itself and used to recycle nearly 100% of the recovered material into the bath. This can save materials and reduce costs to the greatest extent.
E-coating and plating
- What is electro-coating?
- How does electronic coating work?
- What are the benefits of electronic coating?
- How many steps are there in the electronic painting process?
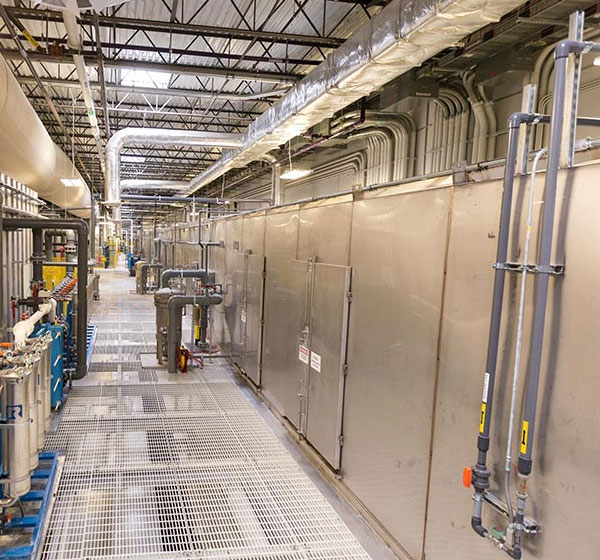
What is electro-coating?
E coating is an immersion wet paint finishing process that uses electric current to attract paint products to certain metal surfaces. This method is also called paint deposition. The E-coating process is a dip coating (immersion) system, which is very similar to the immersion system used in metal electroplating. The difference is that the conclusion drawn is that organic coating particles are used in the immersion bath instead of Metal particles.
How does electronic coating work?
E coating applications use paint particles suspended in a water bath. Instead, the invoiced parts are reduced to the paint tank, and the paint particles are also attracted to the metal parts. The paint particles are formed on all surfaces of the metal parts, thereby forming a flat, continuous, low-key film on the entire surface. The method continues until the preferred film thickness is reached. The film thickness is controlled by the applied current difference.
Focusing on the key to the opposite attraction, the e coating system applies an electric charge to the metal parts and even immerses the fluid in the tank. Then, the paint will be attracted by grounding. This step can be performed in either case, but you will find the benefits of grounding the part (-) and charging the answer (+). Make each component (+) billed as positive, and the tank solution has a negative charge (-). Regarding the polarity from the charge, an anode method or a cathode method can be used as the electronic coating.
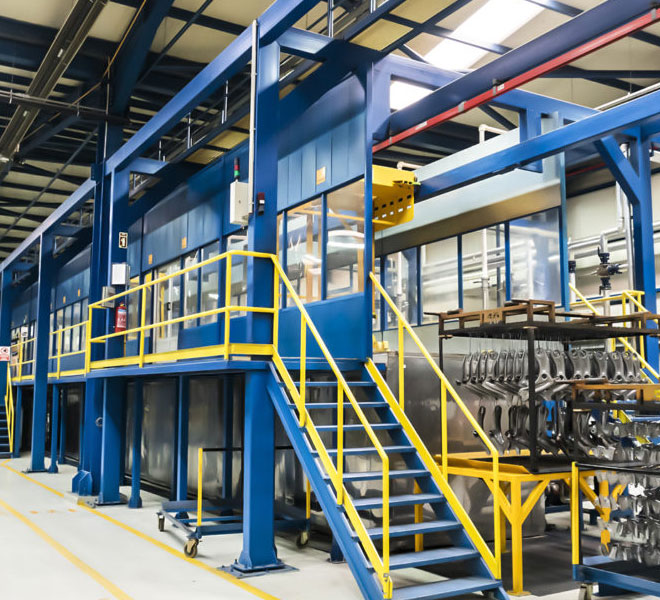
What are the benefits of electronic coating?
E coating has many benefits, including cost efficiency, production line productivity, and environmental advantages. The cost-effectiveness of e coating is higher transfer efficiency, precise film formation control, and lower manpower requirements. The increase in production line productivity in e coating is attributed to faster production line speeds, dense parts erection, uneven production line loads, and reduced human fatigue or errors. The advantages of environmental protection are no or low VOC and HAP products, no heavy metal products, reducing workers’ exposure to harmful substances, reducing fire hazards, and reducing waste emissions.
How many steps are in the electronic coating process?
For the key to the whole electroplating process, namely pretreatment and cleaning, the number of the whole steps may vary from line to line. Regarding listing all the different steps in the process, the Hartford Finishing production line will be used as a reference, but remember that not every e-coat production line includes each of these stages.
E coating process:
- Pendant
- Pretreatment and cleaning
- Paint spraying and flushing
- Lack of liquid oven
- Industrial Oven
In a typical e coating process, the parts are first cleaned and pretreated with a phosphate conversion coating to prepare the parts for e-coat. Then immerse the part in the paint tank, and apply a direct current between the part and the “counter” electrode. The paint is attracted to the part by the electric field and deposited on the part. The parts are removed from the bath, rinsed to recover undeposited paint solids, and then baked to cure the paint.
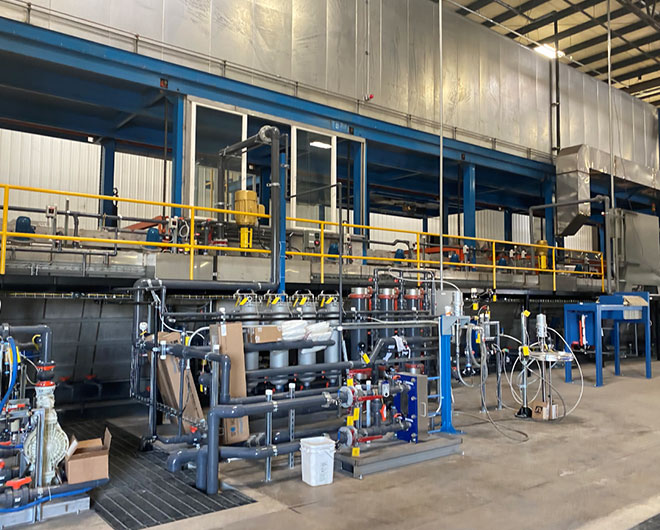