If you are feeling a problem with the inbound and outbound operations of logistics warehouses, why not consider “warehouse automation”? Productivity and operational quality will be improved by an automatic warehouse system that stores and carries luggage on a shelf called a stacker rack, and an automatic conveying robot.
This article describes how to automate warehouses and what is automated storage system, their advantages and disadvantages, and how they were successfully deployed.
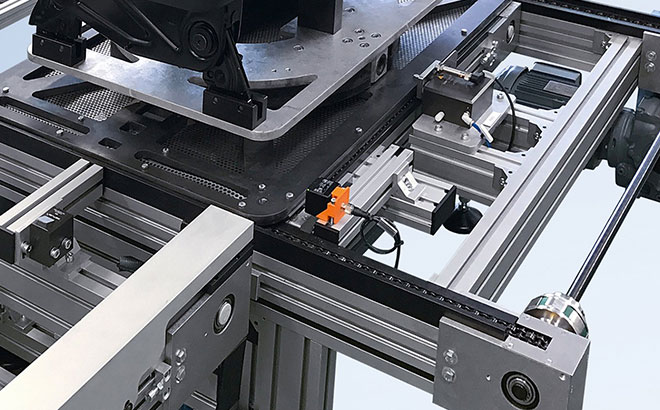
What is an Automated Warehouse?
An automated storage system is a warehouse that allows goods to be automatically stored and taken out. In the logistics industry, where a shortage of human resources is a challenge, the automation of warehouses is attracting a lot of attention.
How the Automate Storage System Operate?
Here’s how to automate your warehouse operations:
- Automatic warehouse system
- Automatic conveyance robot
- Picking system
- Warehouse Management System (WMS)
Automatic Warehouse System Types
An automated warehouse system is a system that automates the flow from receipt to shipment. The package in the warehouse is stored in a moving rack in a warehouse called a stacker rack and is controlled by a computer. This computer is called an “automation system” and centrally manages incoming and outbound information.
In general, automated warehousing systems require stacker racks, stacker cranes, controls, inventory management equipment, and more. Consider carefully because of the cost of deployment.
Depending on the shape of the warehouse and the products handled, the automatic warehouse system can be mainly grouped into the following types:
- Pallet type
Pallet-type automated warehouses are systems for storing products in racks on a pallet-by-pallet basis. Pallets such as the pallet lift modules are stored in high-rise racks, so you can make the most of your high-rise warehouse.
- Bucket type
A bucket-type automated warehouse is a system that stores products in buckets and in racks. Suitable for storing indeterptered products and parts. Because it is stored in a fixed bucket, it looks neat.
- One-Size-Fits-All Type
A one-size-fits-all automated warehouse is a system that stores products of various sizes and stores them in a rack. Since products of different sizes and types can be stored together, it is convenient when handling a large number of products or handling special products.
- Mobile Shelf Type
A mobile shelf type automated warehouse such as the Vertical Carousels is a system that uses electric mobile shelves to store products. Since the shelves themselves can be moved, it is easier to secure aisles than ordinary shelves and space can be used effectively.
- Automatic Transfer Robot
In recent years, the use of automatic transfer robots and AI is increasing in warehouses. There are various types of automatic transfer robots, such as a type in which a small robot sneaks under the rack and lifts it. The automatic transfer robot eliminates the need for employees to roam the warehouse and allows picking at the work station.
- Picking System
A picking system refers to all systems that improve picking efficiency, and generally uses a handy terminal to read barcodes. It scans the barcode, counts the number of stocks, and automatically totals them. The storage location of the product can be grasped in real time.
There is also a system that gives voice picking instructions. If you wear a headset, you can pick without having a list. There is also a system in which a digital display board is installed on the shelves where products are stored to display the quantity and instruct picking.
- Warehouse Management System (WMS)
The warehouse management system is a system that streamlines operations such as inventory quantity, arrival / shipment, inspection, and picking in the warehouse. For example, manage the progress of receipt / shipment work and issue a delivery note.
By linking with the inventory management system, you can grasp the total number of inventory even if there are multiple bases, and you can manage inventory by location. It can also be linked with a sales management system, etc., and warehouse management that suits your business format will be realized.
Advantages and disadvantages of Automation Storage System in Warehouse
Next, let’s look at the advantages and disadvantages of automating warehousing operations.
Benefits: Increased productivity
By automating the warehousing operations that people have been doing, such as warehousing and picking, the burden on employees can be reduced and time can be devoted to important tasks. Especially in warehouses where dangerous goods are stored, if the work is entrusted to the machine, it will help ensure the safety of employees. Also, in the case of a refrigerated warehouse, employees cannot work for a long time and have to take turns, but with the introduction of robots, they can operate 24 hours a day.
In addition, stepping into warehouse automation is an opportunity to improve your business. This is because it is necessary to understand the issues in the field and review the work so far when introducing it. With the introduction, if all employees work together to solve problems, a sense of solidarity will be created and productivity will improve.
Benefits: Stable quality
When 100% accuracy is required, the stress and burden on employees increases, and mistakes are more likely to occur. Automation of warehousing operations will inevitably reduce mistakes and improve operational quality. You can also reduce training and education costs because you can work regardless of employee skills.
Not only business quality but also product quality will be stable. For example, automating operations in a refrigerated warehouse reduces the number of people coming and going, keeps a constant temperature, and makes it difficult for germs to invade from the outside, creating a hygienic environment. In addition, it is also an advantage to be able to thoroughly carry out first-in first-out to prevent human error such as mistakes in taking.
Disadvantages: High installation cost
The biggest disadvantage is the high installation cost. In order to automate warehousing operations, it is essential to introduce various equipment and systems. Depending on the product, the number of inventories may fluctuate greatly due to the influence of the season, so a highly flexible system that can handle expansion of scale is required.
It is a good idea to estimate and consider how long it will take to recover the installation cost. For small and medium-sized enterprises with limited financial resources, it is also effective to rent an automated warehouse from another company. Since the warehouse operations will be outsourced, there is no need to build equipment, and the initial cost can be significantly reduced. It will also solve the problem of labor shortage.
Disadvantage: There is a risk of business suspension in case of trouble
Since automated warehouses are system-controlled, operations may stop if something goes wrong. If business is stopped for even one day, the damage will be great. When installing, build a backup mechanism at the same time, and make a manual for what to do when a problem occurs.
Automate Warehouse Operations and Improve Operational Efficiency
Warehouse automation is made possible by automated warehouse systems, automated transport robots, picking systems, warehouse management systems, and more. Automation can increase productivity and improve logistics quality. However, please note that the installation is costly and there is a risk of business interruption in case of trouble. Improve your work efficiency by automating your warehouse operations in a way that suits your company.