The root cause of Conveyor belt deviation is that the external force on the belt is not zero in the direction of the belt width, or the tensile stress perpendicular to the belt width is not uniform, resulting in the counterforce on the belt from the rollers or rollers, etc. to produce a parting force to one side, which causes the belt to deviate to one side under the action of this parting force. The common runout phenomenon is as follows.
Analysis of the causes of conveyor belt deviation
- The installation is not in place so that the center of the head, tail, and middle frame is not in a straight line.
- The installation position of the drum is not correct, causing the belt to deviate at the drum.
- The belt run out in the middle of the belt due to incorrect jointing of the belt.
- Conveyor belt deviation caused by incorrect roller frame or loose bolts fixing the roller frame.
- Belt deflection caused by damage to the conveyor belt.
- Conveyor belt deviation caused by material unloading point, not in the middle of the conveyor belt.
- Conveyor belt deviation caused by the impact of the material. When the material falls onto the belt, the gravity and inertia of the material impact the belt, which may cause the belt to deviate.
- Conveyor belt deviation caused by the accumulation of materials on the roller and the carrier roller;
- Conveyor belt deviation caused by inaccurate installation angle of the roller;
- Belt deflection caused by unqualified belt quality;
- Conveyor belt deviation caused by the installation and commissioning error of belt tensioning device;
- Belt deflection caused by aging and deformation due to long-term use;
- Belt deflection caused by tilting of the frame;
- Conveyor belt deviation caused by serious vibration of equipment;
- Belt deflection caused by the too-small radius of curvature of concave section belt conveyor.
For belt conveyors designed with concave sections, if the radius of curvature of the concave section is too small, if there is no material on the belt when it is started, the belt will bounce up in the concave section area, and the belt will be blown off when it encounters windy weather.
Adjustment measures for conveyor belt deviation
Through the above analysis of the conveyor belt deviation reasons, take the following corresponding measures.
- Adjust the head, tail, and middle frame of the belt conveyor so that the center of the three is in the same straight line.
- Adjust the roller installation position so that the roller axis is perpendicular to the longitudinal centerline of the belt and parallel to the horizontal plane. Take the first roller as an example, if the tape runs off to which side of the bearing seat, which side of the bearing seat to the running direction of the tape, or the other side of the bearing seat to the opposite direction of running. Note, however, that the actual offset between the centerline of the drum and the centerline of the tape must be determined before adjustment to ensure the correct position of the drum after adjustment.
- Cut out the incorrect tape joint and redo the belt joint. In addition, it is best to nail the belt buckle to the length of the slotted rollers to ensure the slotted performance of the tape joint, prevent and reduce pin breakage and avoid torn tape accidents.
- The runout caused by the wrong roller frame can run outside of the roller frame to the tape forward direction to move a little, generally moving a few rollers can correct the deviation. If the deviation is serious, you need to re-calibrate the roller frame so that the error in the level of the roller set is controlled within the permissible deviation. If the conveyor belt deviation is caused by a loose bolt of the fixed roller frame, the loose bolt can be solved by re-tightening it.
- It can be solved by strengthening the inspection and maintenance of the belt and repairing or replacing the damaged belt in time.
- Adjust the position of the discharge point so that it is located in the middle of the tape.
- Use a reasonable structure of the guide plate, to avoid large blocks or a large height directly under the material, can also be installed in the lower material mouth under several sets of buffer rollers.
- Eliminate the sticky material on the surface of the drum or roller. At the same time, the empty section spring cleaner should be adjusted. The contact length between the cleaner and the conveyor belt systems in the direction of the roller axis should be greater than 85% of the bandwidth to ensure that the material is removed at any time.
- Adjust the roller set to the correct position. When the middle part of the belt conveyor runs off the belt, the installation holes on both sides of the roller support can be modified and processed to make it a longer hole, when the belt deviates to the left side, the left side of the roller set moves forward towards the belt running direction, or the right side moves back; when the belt deviates to the right side, the right side of the roller set moves forward towards the belt running direction, or the left side moves back.
- Users should choose manufacturers with a good reputation and rich production experience, and at the same time equipped with perfect technical service personnel, who can solve users’ usage problems in time and implement good three-package service of the products.
- When installing the tensioning device, the centerline of the belt conveyor and the axis of the drum of the tensioning device should be vertical. Operators should strictly follow the installation requirements and do the debugging work.
- The belt conveyor should be overhauled after a period of use, and the belt should be replaced in time foraging and deformation.
- Correct the skewed frame. Skewed racks include skewed rack centerline and both sides of the rack height tilt, can only be re-installed through the rack to ensure that the rack centerline and both sides of the rack are flat, to fundamentally solve the problem.
- Find out the cause of vibration and solve it in time.
- It is best to install additional pressure pulleys at the concave section of the belt conveyor to avoid the belt bouncing or being deflected by the wind. A larger radius of curvature of the concave section should be used as far as possible at the design stage to avoid such situations.
During the operation of the belt conveyor, attention should be paid to the deviation of the belt, the causes of the deviation should be correctly judged and appropriate measures should be taken in time to ensure the safe, efficient and stable operation of the belt conveyor. When available and capable, an anti-divergence switch can be used or a travel switch can be designed as a safety protection alarm device to fundamentally eliminate tape runout faults, prevent material leakage and abnormal damage to the equipment and ensure the productivity of the equipment.
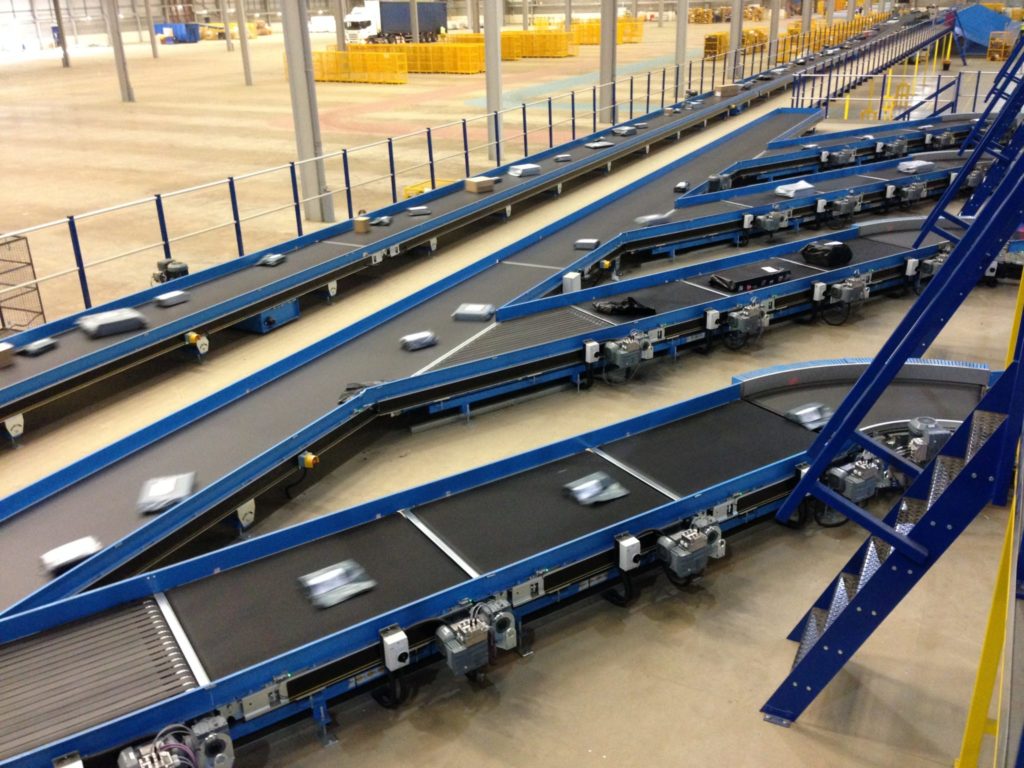