Assembly line is manufacturing systems in which work-in-process moves in a sequential manner from one station to another. At each station, new parts are added or new assemblies are made, resulting in a finished product.
Assembly line production definition is manufacturing systems in which work-in-process moves in a sequential manner from one station to another. Assembly speeds up the entire manufacturing process by transferring semi-finished products from one process to another. This is a dramatic improvement over previous methods in which complex production routes and disconnected processes added to the complexity of assembly. In addition, the assembly line process enable workers to develop process-specific expertise, which helps the entire line work more efficiently. As a result, manufacturers can complete complex products, such as automobiles, aircraft, and industrial machines, at higher speeds and with greater precision than ever before.
Types of the assembly line
Assembly line vary depending on who is using them and for what purpose. They are usually tailored to the product being produced. However, they fall broadly into the following categories.
- Automated: These assembly lines are operated primarily by and with the help of machine manuals, rather than by hand. Most assembly line are automated.
- Classic: Classic assembly line use a series of steps and different individuals to manufacture a product, such as a car.
- Intermittent: This type of assembly line produces similar but not identical products. For example, the furniture industry may use intermittent assembly lines to produce parts with different types of interiors.
- Lean: Similar to an automated line, this line involves the use of a group of workers rather than one or two people.
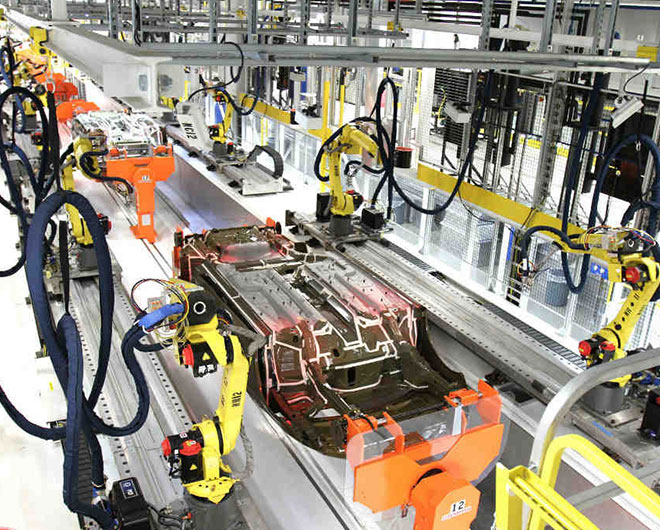
Basic advantages of the assembly line
- Increased product yield: Automation increases the productivity of parts. This in turn, generates greater profitability.
- Ensure production quality: Robotic assembly and inspection can maximize production and error detection, and use camera-equipped robots for quality assessment and verification. This helps reduce variability, bottlenecks and provide consistent output.
- Increase efficiency: Auto assembly lines allow you to track and trace every cell produced in the manufacturing process. If any problems arise, you will be able to examine every action taken to find the root cause of the problem and resolve it. As a result, it saves time and labor.
- Standardized production: The process is executed reliably through automation, freeing the operator from hours of tedious and challenging manual tasks. Automation is precise and repeatable. It ensures that each product is manufactured with the same specifications and processes.
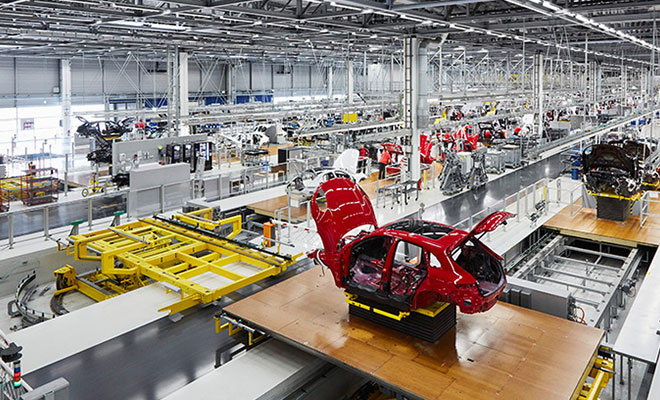
Features of Modern Assembly Lines System
Data collection
On modern assembly lines, new sensors and industrial IoT devices collect data from people and machines in real time.
Cooperation
Thanks to advanced robotics, collaborative automation, and more sophisticated software, the working relationship between man and machine on the assembly line are closer than ever before.
Less linear
Some assembly lines are not as linear as their predecessors. Instead, work will be dynamically routed between different rows and cells as needed.
High-Mix products
Due to the high demand for customization and more advanced error-proofing technology, modern assembly lines can produce hundreds of variants of a single product.
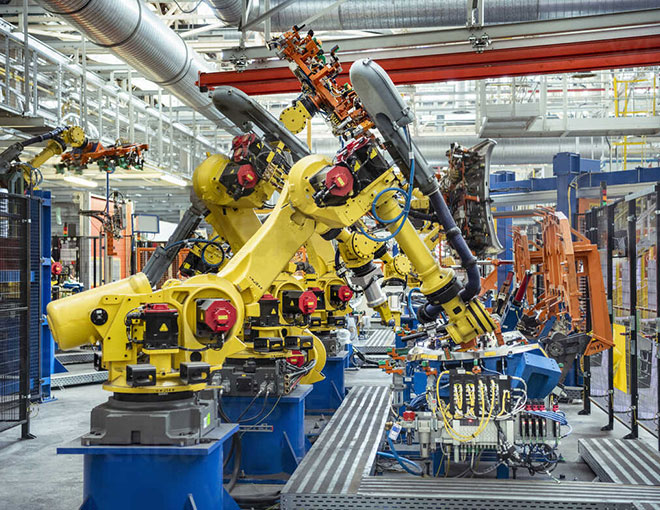